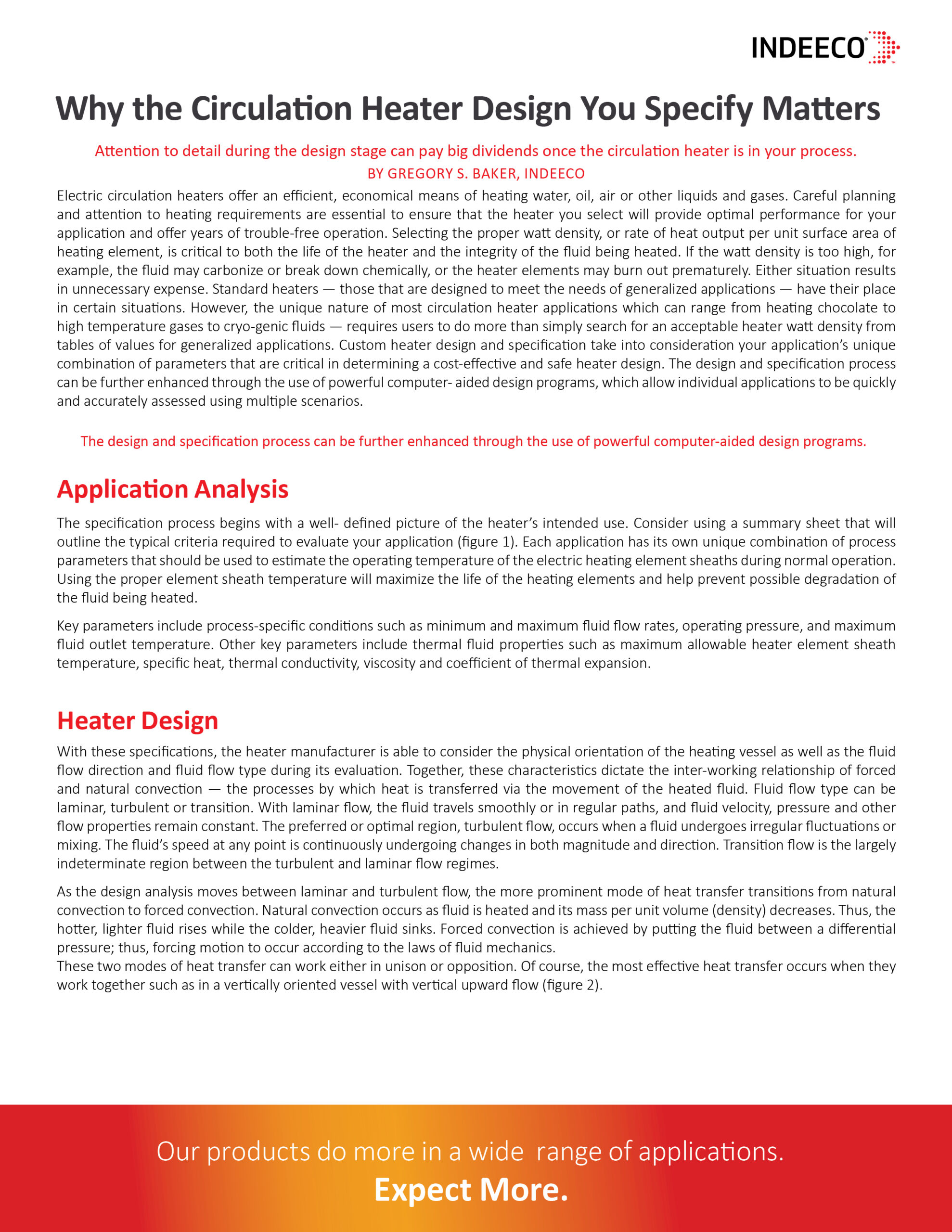
Electric circulation heaters offer an efficient, economical means of heating water, oil, air or other liquids and gases. Careful planning and attention to heating requirements are essential to ensure that the heater you select will provide optimal performance for your application and offer years of trouble-free operation.
Selecting the proper watt density, or rate of heat output per unit surface area of heating element, is critical to both the life of the heater and the integrity of the fluid being heated. If the watt density is too high, for example, the fluid may carbonize or break down chemically, or the heater elements may burn out prematurely. Either situation results in unnecessary expense. Standard heaters — those that are designed to meet the needs of generalized applications — have their place in certain situations. How-ever, the unique nature of most circulation heater applications — which can range from heating chocolate to high temperature gases to cryogenic fluids — requires users to do more than simply search for an acceptable heater watt density from tables of values for generalized applications. Custom heater design and specification take into consideration your application’s unique combination of parameters that are critical in determining a cost-effective and safe heater design. The design and specification process can be further enhanced through the use of powerful computer aided design programs, which allow individual applications to be quickly and accurately assessed using multiple scenarios.
Application Analysis
The specification process begins with a well defined picture of the heater’s intended use. Consider using a summary sheet that will outline the typical criteria required to evaluate your application (figure 1). Each application has its own unique combination of process parameters that should be used to estimate the operating temperature of the electric heating element sheaths during normal operation. Using the proper element sheath temperature will maximize the life of the heating elements and help prevent possible degradation of the fluid being heated. Key parameters include process-specific conditions such as minimum and maximum fluid flow rates, operating pressure, and maximum fluid outlet temperature. Other key parameters include thermal fluid properties such as maximum allowable heater element sheath temperature, specific heat, thermal conductivity, viscosity and coefficient of thermal expansion.
Heater Design
With these specifications, the heater manufacturer is able to consider the physical orientation of the heating vessel as well as the fluid flow direction and fluid flow type during its evaluation. Together, these characteristics dictate the interworking relationship of forced and natural convection — the processes by which heat is transferred via the movement of the heated fluid. Fluid flow type can be laminar, turbulent or transition. With laminar flow, the fluid travels smoothly or in regular paths, and fluid velocity, pressure and other flow properties remain constant. The preferred or optimal region, turbulent flow, occurs when a fluid undergoes irregular fluctuations or mixing. The fluid’s speed at any point is continuously undergoing changes in both magnitude and direction. Transition flow is the largely indeterminate region between the turbulent and laminar flow regimes. As the design analysis moves between laminar and turbulent flow, the more prominent mode of heat transfer transitions from natural convection to forced convection. Natural convection occurs as a fluid is heated and its mass per unit volume (density) decreases. Thus, the hotter, lighter fluid rises while the colder, heavier fluid sinks. Forced convection is achieved by putting the fluid between a differential pressure; thus, forcing motion to occur according to the laws of fluid mechanics. These two modes of heat transfer can work either in unison or opposition. Of course, the most effective heat transfer occurs when they work together such as in a vertically oriented vessel with vertical upward flow (figure 2). Because laminar flow requires considerable length to become fully developed and typical electric heat exchangers are relatively short with element bundle-support spacers that interrupt the flow, pure laminar flow is rare. Extensive empirical data exists to support fully turbulent and fully developed laminar flow regimes as well as pure natural convection. However, in most real world applications, one mode of heat transfer will dominate or the resultant mode of heat transfer will be a combination of the types. Properly understanding and applying these heat transfer phenomena can dramatically affect which watt density you select for your circulation heater application. For example, in higher temperature gas applications, the acceptable watt density can be greatly improved by designing the heater’s geometry (i.e., shell diameter and baffling types) to ensure that the flow regime within the heater vessel is in the turbulent region.
Heater Optimization
With the widely accepted use of computer-aided design tools in today’s engineering, the complicated iterations involved in evaluating criteria for circulation heater selection have been greatly facilitated. Individual applications can be quickly and accurately assessed using multiple scenarios to determine the optimal design options based upon your current and future heating needs. A heater manufacturer can, for example, simulate a seamless transition from no-flow to high-flow conditions that accounts for forced convection in laminar, transition and turbulent flow regimes in addition to natural convection. Geometry plays an important role in heat transfer: Vertical and horizontal installations have different natural convection heat transfer characteristics. Computer-aided design tools can account for vessel orientation and flow direction. Computer-aided design programs also assist in the calculation of pressure drop, which generally acts inversely to heat transfer, for a given geomertry. In gas applications, heater vessel shell temperature calculations take into account the additional heat radiating from the heating elements — which can be extremely dangerous if overlooked — and high-pressure effects on gas properties (heat capacity, thermal conductivity and viscosity). Employing computer aided design programs to manipulate the heater’s physical design and optimize these critical design parameters will provide the best engineered and most economical circulation heater for your specific application.
Attention to detail during the design stage can pay big dividends once the circulation heater is in your process.
BY GREGORY S. BAKER, INDEECO