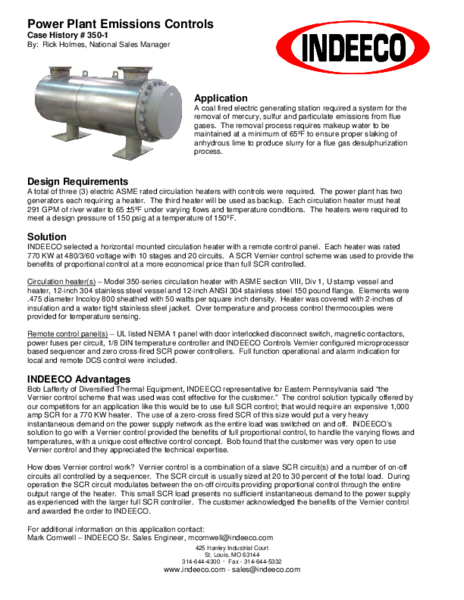
A coal fired electric generating station required a system for the removal of mercury, sulfur and particulate emissions from flue gases. The removal process requires makeup water to be maintained at a minimum of 65ºF to ensure proper slaking of anhydrous lime to produce slurry for a flue gas desulphurization process.
Design Requirements
A total of three (3) electric ASME rated circulation heaters with controls were required. The power plant has two generators each requiring a heater. The third heater will be used as backup. Each circulation heater must heat 291 GPM of river water to 65 ±5ºF under varying flows and temperature conditions. The heaters were required to meet a design pressure of 150 psig at a temperature of 150ºF.
Solution
Indeeco selected a horizontal mounted circulation heater with a remote control panel. Each heater was rated 770 KW at 480/3/60 voltage with 10 stages and 20 circuits. A SCR Vernier control scheme was used to provide the benefits of proportional control at a more economical price than full SCR controlled.
Circulation heater(s) – Model 350-series circulation heater with ASME section VIII, Div 1, U stamp vessel and heater, 12-inch 304 stainless steel vessel and 12-inch ANSI 304 stainless steel 150 pound flange. Elements were .475 diameter Incoloy 800 sheathed with 50 watts per square inch density. Heater was covered with 2-inches of insulation and a water tight stainless steel jacket. Over temperature and process control thermocouples were provided for temperature sensing.
Remote control panel(s) – UL listed NEMA 1 panel with door interlocked disconnect switch, magnetic contactors, power fuses per circuit, 1/8 DIN temperature controller and Indeeco Controls Vernier configured microprocessor based sequencer and zero cross-fired SCR power controllers. Full function operational and alarm indication for local and remote DCS control were included.
Indeeco Advantages
Bob Lafferty of Diversified Thermal Equipment, Indeeco representative for Eastern Pennsylvania said “the Vernier control scheme that was used was cost effective for the customer.” The control solution typically offered by our competitors for an application like this would be to use full SCR control; that would require an expensive 1,000 amp SCR for a 770 KW heater. The use of a zero-cross fired SCR of this size would put a very heavy instantaneous demand on the power supply network as the entire load was switched on and off. Indeeco’s solution to go with a Vernier control provided the benefits of full proportional control, to handle the varying flows and temperatures, with a unique cost effective control concept. Bob found that the customer was very open to use Vernier control and they appreciated the technical expertise.
How does Vernier control work? Vernier control is a combination of a slave SCR circuit(s) and a number of on-off circuits all controlled by a sequencer. The SCR circuit is usually sized at 20 to 30 percent of the total load. During operation the SCR circuit modulates between the on-off circuits providing proportional control through the entire output range of the heater. This small SCR load presents no sufficient instantaneous demand to the power supply as experienced with the larger full SCR controller. The customer acknowledged the benefits of the Vernier control and awarded the order to Indeeco.