Automated Control of Heat-Treating Processes: Technology, Data Acquisition, Maintenance and Productivity Gains
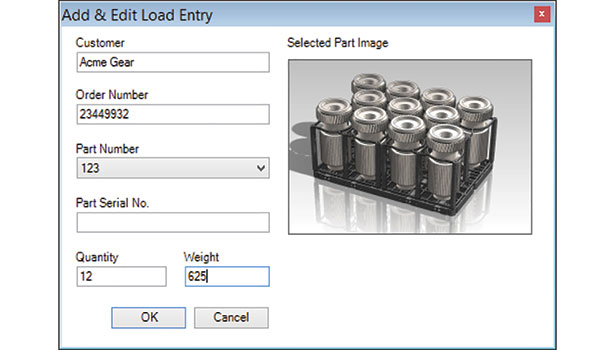
Read an article about heat-treating processes and how diverse they can be!
Technology and Productivity Gains
Technology has played a major role in nearly all aspects of achieving higher quality and greater efficiency in heat-treating processes. These and other factors help drive customer demands for higher quality and faster delivery. The challenge for many heat treaters is meeting such demands while justifying the cost of implementing the technology that makes it possible. Many heat treaters use incremental improvements to existing technology to yield positive results. In this context, incremental improvements are steps to automation. The first step may be automated recipe controls retrofitted into an existing control cabinet. A typical next step would be a plant-wide Supervisory Control and Data Acquisition (SCADA) system providing widely enhanced visibility to what is happening on the shop floor.
Better technology allows for greater trust in the heat-treating process. In addition, it gives the heat treater the opportunity to free up resources for different tasks.
Data Acquisition
Data acquisition, the logging of process-related data for later analysis, has been around for a very long time. Historically, it existed with paper chart recorders and has evolved into electronic, computerized formats providing information to all areas of the business. It is almost impossible to read an article related to data acquisition (or to information technology in general) and not see the term big data. This term implies the fact that we are gathering more information than ever before. The challenge, naturally, becomes putting that information to good use.
What makes data “usable” is specific to each operation, and each operation is different. Business drivers in heat treating tend to be initiated from quality control, where electronic information requirements provide proof of traceability or of meeting industry requirements such as CQI-9 and AMS 2750. We find that quality is the biggest driver for investments in data-acquisition technology, but the benefits should not stop there. Every part of the business – operations, quality, sales and maintenance – can benefit from a data-acquisition strategy. Information can be gathered from all areas of a business and evaluated holistically to make better decisions on current operations.
Benefits to Maintenance
Preventive-maintenance programs are common to all heat-treating operations, and all of them are well-intentioned. In our experience, a large percentage of maintenance is reactive. When maintenance is reactive, unplanned downtime takes place with a significant impact on production planning as well as the possible load impact of rework or scrap parts. Preventive maintenance is planned, with planned activities and planned downtime that allow the maintenance department to work around production schedules. Data-acquisition and control technology both provide additional parameters (for example, the operating time of an element, pump or burner or the number of times a door has been opened and closed) useful for ensuring that maintenance is less reactive and more preventive.
Read more here.
Contact an INDEECO Representative https://indeeco.com/ today to discuss heat-treating processes that could benefit your industry!