SPECIAL FOCUS: Infrared Heating Infrared HEATS UP
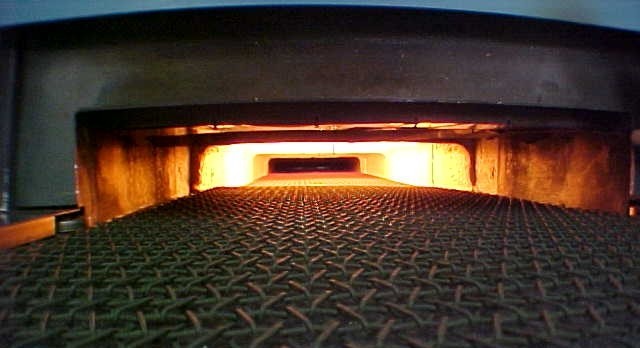
Infrared (IR) technology is currently used in a wide range of industrial applications such as:
- The electronics industry for drying solder resists
- Food processing for browning and sterilization
- Coating/finishing for drying and curing
- Textiles for drying and sealing
- Plastics for softening
- Printing for drying
- Manufacturing/engineering for degreasing, preheating, and shrink fitting
Infrared energy causes the surface electrons of an object to excite and oscillate, creating heat. Several factors determine the temperature, not the least of which being the wavelength of the electromagnetic radiation generated by the infrared heating source. The equipment used for the above applications utilizes medium and long wavelength IR and is typically capable of less than 800°F (427°C). Since the wavelength is inversely proportional to the temperature, the wavelength shortens as the temperature goes up [2].
The high temperature infrared processing discussed here primarily utilizes short wavelength T-3 tungsten-halogen lamp-based systems with unique designs to enable the systems to operate at higher temperatures in industrial environments. Infrared heating has many advantages over other heating techniques. It provides:
- An inherently clean non-contact heating method
- Rapid response energy fluxes capable of heating rates in excess of 50°C/s (material and mass dependent)
- Excellent spatial and tempered control allowing sample-only heating uni-directionally over large areas
- Rapid power level changes due to low thermal mass (halogen lamps)
- Rapid cooling rates due to the “cold wall” nature of IR
- Controllable temperature gradient processing up to flux densities of 50 W/cm2
Thus, infrared provides a versatile and flexible answer to heat transfer problems throughout the industrial spectrum [3].
Read more here.
For more information: The Infrared Division of IHEA (IRED) recently published a handbook that explains the benefits of infrared for industrial applications.