The Five P’s of Maintenance Shutdown
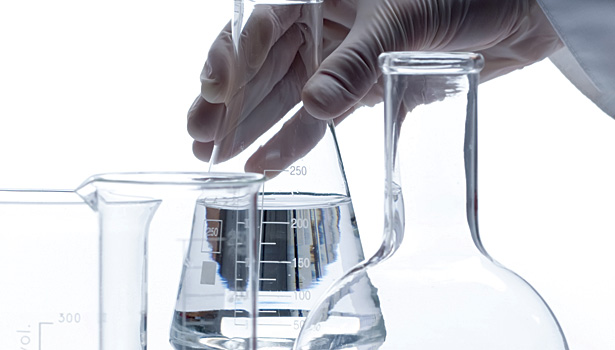
This article gives great advice on when shutting down for regular scheduled maintenance. Follow the five P’s of maintenance shutdown for a smooth and easy going experience.
Routine maintenance shutdowns of thermal fluid systems involve a staged process before, during and after the operation to reduce the amount of idle time incurred in the plant. Some jobs need to be organized well in advance to get the right equipment in place as well as replacement components. This allows each task to be run more efficiently and avoids having to shut the plant down more than once.
Three months prior to shutdown, plant engineers should check pressure relief valve tags and certificates for when they are due for testing. If the test is due within a 12-month period of the next planned shutdown, arrangements should be made for testing or replacing. The system will need to be partially drained for this to be carried out. During the shutdown, the valve can be tested, tagged and the certificate retained. New Call-to-action
One month prior to shutdown, arrangements should be made for thermal fluid to top up the system. For many companies, this is the only planned shutdown for the year —and the only time the thermal fluid is cooled to an ambient temperature. Once cooled, thermal fluid can reduce its volume by up to 30 percent (depending on fluid type) from its hot volume, taking the system off the low level and requiring topping up.
During the main shutdown, the header tank should be checked for cleanliness when the system is drained. Plant engineers may need to be prepared for urgent cleaning of the header tank to remove residues that may have built up. High and low level fluid sensors also need to be checked as well as pipework for correct working flow.
Dump and overflow tanks need to be checked for their contents and arrangements made for them to be drained. Plant engineers also should inspect strainers and clean filters if fitted. If no filters are fitted, they should consider refitting them after any work on the system has been carried out to protect the pumps. After running the system cold for a few hours, the filter can then be removed and the system can run as normal.
The expansion tank is critical to the operation of the system. Its main purpose is to allow a place for the heat transfer fluid to expand into when heated, and a source to draw fluid away from to keep the system full when cooled. It also has a built-in reserve tank in case there is a small leak as it keeps the system full.
Ultimately, if engineers remember the five P’s of maintenance shutdowns — prior preparation prevents poor performance — this complex process will become manageable. Shutdowns may become so routine and seamless that the interruption becomes a productive part of the process. Good planning will save the costs of downtime and, in the long term, reduce maintenance bills.
Read more here.
For more advice on maintenance shutdown contact Indeeco https://indeeco.com/.