Short-Wave Infrared Speeds Up Aerospace Tool Heating
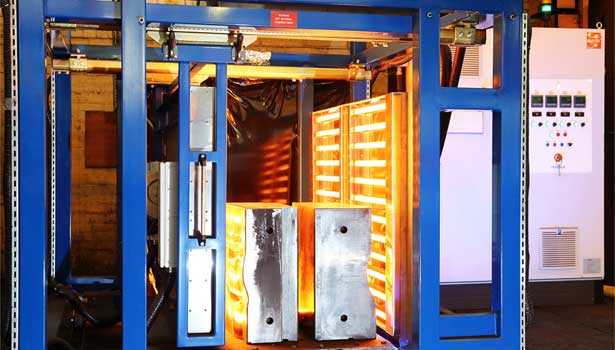
This article discusses two different ways that infrared (IR) heating can be used. One is a high-heat process requiring preheating of the tools/dies, and the other is a lower-temperature process where IR is cleaner and more efficient. Can infrared be used in your process to improve energy efficiency?
Short-wave infrared emitters have allowed Mettis Aerospace to reduce the time required for the heating of tools and dies used in the manufacture of high-specification titanium aircraft components to one-seventh of the heating times required by a previous gas system. This has provided significant energy savings and improved controllability, as well as improved forging practices, at the company’s Redditch (U.K.) site.
Mettis Aerospace has decades of experience in the production of highly complex, forged and machined, safety-critical aircraft components. This extends from manufacturing the majority of Britain’s aero-engine pistons during WWII to pioneering the use of titanium in jet engines to developing alloys for use in Concorde’s structure and skin. Today, Mettis is an important global supplier of complex alloy components to industry giants such as Rolls-Royce, Boeing and Airbus.
Titanium
The manufacture of titanium components involves heating titanium preforms to above 900°C (1652°F) and then transferring the heated material into molding tools. However, it is essential that the tools are preheated to above 200°C (392°F) to allow better material flow and avoid die wear. Previously, die heating had been carried out by an open-flame gas system, which directed its heat onto support plates. The gas system remained switched on for 24 hours to ensure that the plates were at the correct temperature before the tools were loaded into position. Heating by this method could take up to 10 hours, with limited control of the heat transfer.
When modernization work was carried out in the Redditch facility, particular attention was paid to the tool-heating system, and Heraeus Noblelight was asked to provide an alternative infrared solution. The short-wave system installed consists of two 72-kW infrared cassettes, each mounted on an aluminum vertical profile frame. The two frames are positioned on either side of the table used to support the tools, which can be heated in pairs or individually with heat applied from one side only or from both sides. During heating, a pair of thermocouples measures the temperature of each tool face, and this measurement is then used to automatically regulate each cassette’s emitters constantly from 0-100% to maintain the set temperature with optimum energy consumption, maximizing the system’s efficiency.
Since installation, the new system has allowed significant energy savings because it is now only switched on when required. Tool heating times have been reduced, in some cases, from 10 hours to just 90 minutes.
Read more here.
For more information: Contact Ian Bartley, Heraeus Noblelight Ltd, Unit 1, Millennium Court, Clayhill Industrial Estate, Buildwas Rd., Neston, Cheshire CH64 3UZ; tel: 0151 353 2710; fax: 0151 353 2719; e-mail: ian.bartley@heraeus.com