Comparing Heat Sources
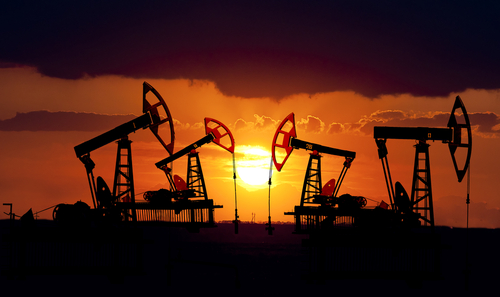
When comparing heat sources used for drying processes there are a few variables: the primary carriers are usually solid or gaseous but may take the form of waves or other radio frequency technologies.
Fossil fuels constitute the majority of commercially available energy sources used to generate heat. The supply of these fuels is diminishing, however, without a viable alternative having yet been fully developed or accepted.
Most fuels contain carbon and hydrogen; therefore, they are collectively termed hydrocarbons. Grouped by form into solid, liquid and gaseous fuels, each form has its own unique idiosyncrasies and peculiarities.
Generally, the cost of using a given fuel is dictated by logistics. Solid fuels must be stored, and the investment for ash and other required materials-handling and pollution-control systems can be high. Liquid fuels also must be stored and pumped, and in some applications, require heating before they can be used. Pollution control requirements typically are less with lighter and cleaner fuels. Also, gaseous and liquid fuel efficiency is higher than solid fuels because the excess air requirements to ensure complete combustion are less. (Therefore, there are smaller losses.)
Solid Fuels
Where coal is a freely available, it is a relatively inexpensive energy source. Obtainable in many grades and sizes, its quality and calorific value as well as the consistency of the particle size distribution largely determine its cost. As a rule, finer and more consistently sized coal is more expensive. Beyond the normal products of combustion, some coals may have a particularly high sulfur level, which can lead to equipment corrosion problems if high enough concentrations of acid are allowed to form. Logistics and distribution may contribute additional costs to using this fuel.
Coal commonly is combusted using pulverized fuel burners, liquidized bed combustors or stokers such as a chain grate underfeed stoker. Particle size and capital investment restrictions are the major influencing factors in the selection process.
As with most combustion processes, the temperature of the gases generated during the combustion of coal is high. Introducing these gases, diluted by makeup air, directly into the process would affect a direct-drying system. Operating as an indirect system, the gas gives up its heat to water (steam), thermal oils or gases (nitrogen, air or other gases). In these cases, the primary heat source is coal, and the secondary source is steam, oil or gas. Depending on the dryer type, the steam or oil may need to pass through another heat exchanger to heat another carrier — air, for example — for an air-drying system.
Other possible solid fuel sources include process byproducts and waste materials, which can provide an economic advantage to the process.
Liquid and Gaseous Fuels
Petrochemicals and their derivatives, including natural gas, form the second fuel group. Liquid systems mainly utilize atomizing burner systems while gaseous burners most often incorporate a mixing or turbulent action to improve combustion. Whether burning a liquid or gaseous fuel, the burner requires a combustion chamber — often integral to the dryer, as is the case with certain rotary cascade and fluid bed dryer designs — and a supply of combustion (primary) and excess (secondary) air. As with coal, cleaner, more efficient combustion, which produces minimal losses, occurs near stoichiometric conditions (perfect combustion). Different fuel oils and gases produce different combustion emissions, which can be commercially optimized for the process.
In general, as fuel viscosity increases, cost falls. Correspondingly, as viscosity increases, fuel quality degrades as the combustible product becomes dirtier and more contaminated. As a consequence of the higher viscosity, many of the heavy fuel oils (and some light fuel oils) require an additional heating system to reduce fluid viscosity and enable the oil to flow and be atomized.
Liquid and gaseous fuels are used extensively as direct and indirect heat sources. In direct systems, the combustion and excess air specifications are designed to meet the necessary air requirements of the drying process. With clean-burning gases, the heat source can be used directly on sensitive products without the products of combustion degrading product quality due to contamination. Liquid and gaseous fuels also can be used with a secondary heat source, similar in design to solid-fuel indirect heating systems.
Electricity
Not a fossil fuel but rather a product thereof, electrical heat generation deserves a section of its own. Although electricity often is the most costly energy source per unit output (BTUs or joules), a holistic investigation of the process may present a more favorable outlook. Electrically powered heat-generating equipment frequently offers unmatched versatility.
The range of electrically powered heat-generating equipment available is vast. It includes implicitly direct heat sources such as microwave, infrared, radio frequency and dielectric technology as well as conventional indirect elements such as silicon carbide, In-coloy, and Inconel heaters. A relatively clean fuel, electricity also is effective for indirect applications such as boilers and oil heaters.
Steam
In the same fashion as electricity, steam frequently is referred to as a heat source. Although steam geysers have been successfully harnessed to generate power, it is not common to use naturally occurring steam in industrial applications. Instead, steam typically is generated using combustion or electricity to heat, vaporize and pressurize water.
Most applications employ steam as an indirect source, using either a heat exchanger to transfer heat to a gas carrier or a jacketed vessel or drum to heat a surface. It also is used as a direct heat source to achieve effective drying.
The amount of energy that can be carried by steam is related to the pressure at which the steam is delivered. The higher the pressure, the greater the energy contained. Obviously, as the pressure increases, the steam-generating equipment and associated piping reticulation must be more rugged and robust. This can increase the capital investment significantly.