4 Considerations when Selecting an Electric Immersion Heater
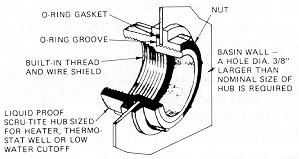
For optimum performance and to maximize service life there are key factors that need to be considered before selecting an immersion heater.
Abstract
Electric immersion heaters are often used in water tanks for freeze protection or to maintain elevated process temperature and in oil tanks to maintain proper viscosity. Because the elements are fully immersed, they are almost 100% efficient, small, and easily controlled. For all but the largest applications and especially when there is a hazardous environment electric heaters are cost competitive. Electric heaters have many advantages over other heating methods such as steam, hot water boiler systems or gas fired pipe heaters. We will look at a few of the basic decisions one must make when selecting an electric immersion heater.
First decisions, watt density and sheath selection
Electric immersion heaters in water tanks can be subjected to prolonged periods of stagnant water with treatment chemicals and contaminants. Selection of the sheath material is an important first consideration because the elevated temperature of the element sheath is a catalyst for accelerated chemical corrosion. Both copper and 304 stainless steel sheathed, compacted tubular heating elements at 50-70 watt/in2 have proved successful in clean water while derating to 20-30 watts/in2 is indicated with significant additives. Incoloy alloys, incoloy 800 or incoloy 840, can be a cost effective alternative over 304 SS or 316 SS in certain corrosive environments, particularly chlorides.
For “clean” water applications or with DI water the sheath material is upgraded to 316 SS often pickled and passivated to remove surface carbon or even electroplated for an almost mirror element surface. Important to note that in some very clean DI water applications metal sheathed elements, no matter how treated, are not recommended.
In oil tanks carbon steel sheaths are appropriate for all but the highest temperature synthetic oils however appropriate watt density becomes critical. With water selecting too high a watt density can accelerate the precipitation of solids on the element but does not harm the water. With hydrocarbons, and their much lower specific heat, too much watt density can cause the oil to “coke” on the heater, reference figure 1.
Figure 1
Watt density is determined by the thermal properties of the oil and the process temperature. In these applications it is the ability of the fluid to accept heat which is the limiting factor in selecting the watt density. In general the heavier the oil the lower this watt density. Electric heater manufacturers can help with the selection process. Indeeco can estimate the sheath watt density provided the fluids properties as indicated in figure 2 below. Contact sales@indeeco.com for additional information.
To continue reading this article, please click on the link below for a free download of this resource.